|
Automation Solutions Conference
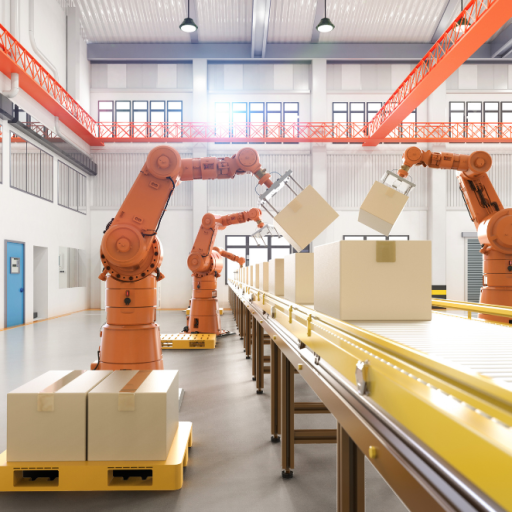
Event Overview
Why Attend
Join MHEDA and your industry peers for a one-day event to start your automation journey beyond the warehousing and distribution sector.
Insight
Engage with like-minded peers looking to expand their business in automation.
Expertise
The conference presenters are MHEDA Members who share experiences and insights.
Knowledge
Gain practical knowledge on providing support and setting realistic expectations.
Network
Connect with industry peers to gain insights and expand your network.
event registration coming soon
Stay tuned for updates and important details, and make sure to check back regularly so you don’t miss out on this opportunity. In the meantime, explore other events and resources designed to help you connect, learn, and thrive in the material handling industry.
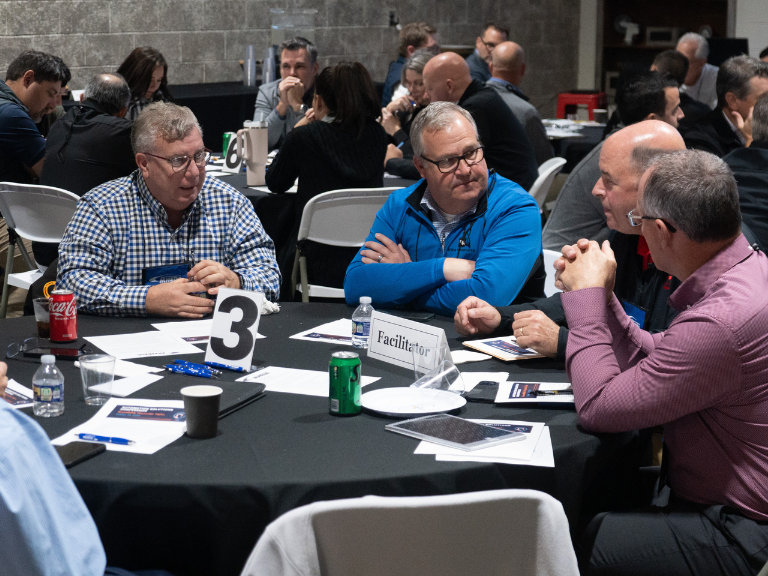
Join industry peers in Atlanta, GA for this one-day conference!
This comprehensive program is designed to equip you with the skills and knowledge needed to succeed in the evolving automation landscape. Gain practical knowledge on providing exceptional support and setting realistic expectations.
Conference Location
Toyota Material Handling Systems
Toyota Material Handling Systems supports warehousing, logistics, manufacturing, distribution and supply chain operations.
Address
6000 Plummer Rd SW
Atlanta, GA 30336
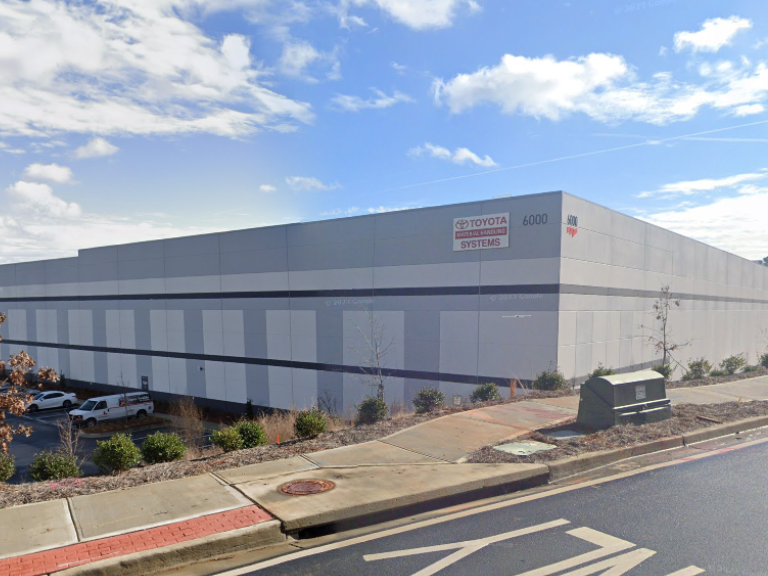
what people are saying
“Great for peer networking, and plenty of industry professionals to learn from. The speakers and flow of topics made it easy to digest for those looking into the automation space.”